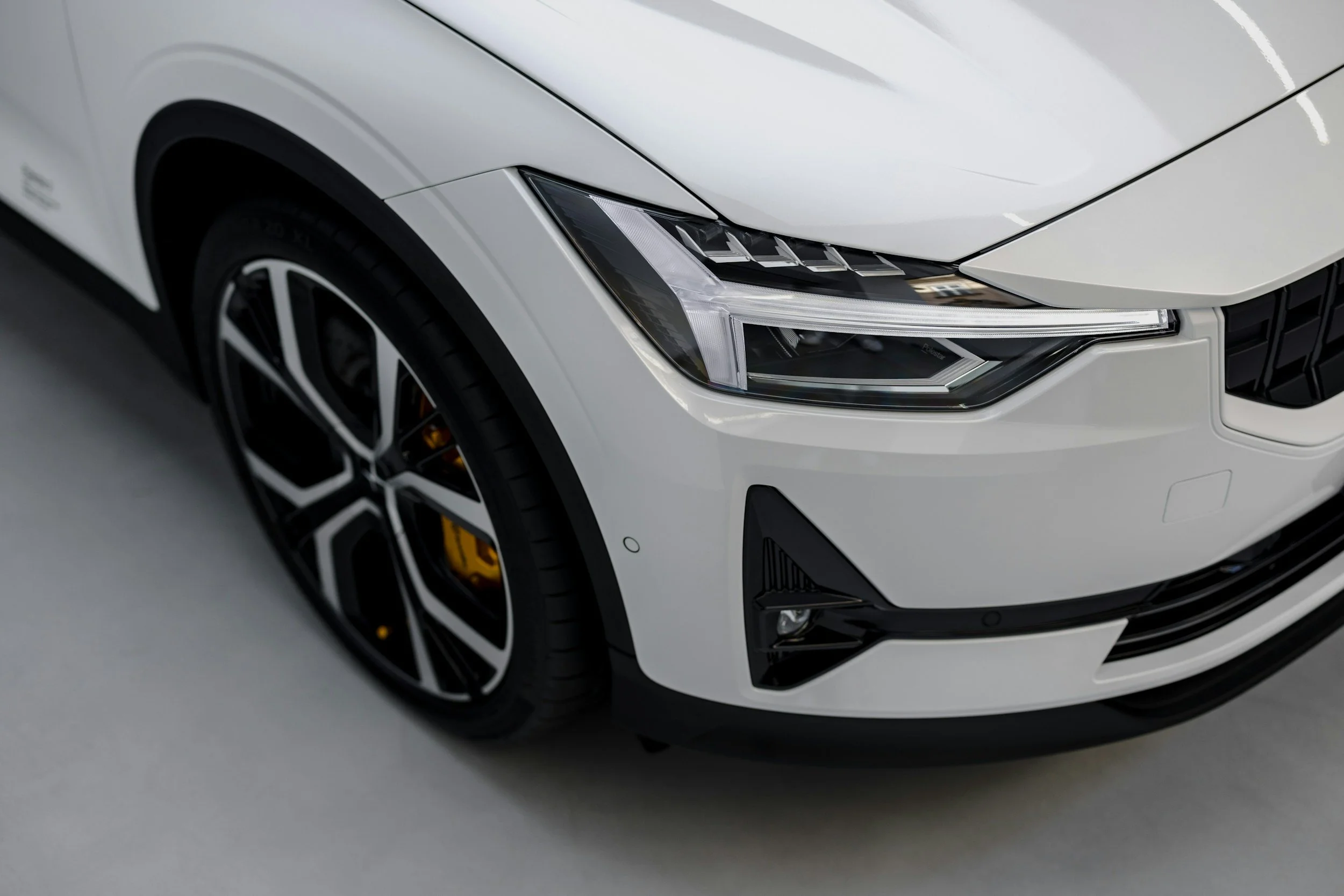
Non-Reactive Adhesive
This thermoplastic adhesive is applied in a molten state and bonds through cooling and solidification.
Productivity
Our non-reactive adhesive accelerates and simplifies the application process, reducing cycle-time and boosting your output
No curing time or equipment cleaning required due to non-reactive formulation
No need for surface preparation of materials
The process can be easily automated with robots and solidifies within minutes after application
It allows for reapplication and disassembly, enabling quick part replacement and material recycling
Flexibility & Sustainability
If the application is imperfect or modifications need to be made, it is easy to peel away and reapply - seamlessly.
Non-reactive adhesives offer significantly magnified flexibility of production processes, timing, and modifications over their reactive counterparts. This translates directly to you in the form of:
Yield rate improvement, reducing unnecessary waste
Repair/re-fit cost reduction, with quick and easy replacement whenever you need it
Easier material recycling, lowering costs and better serving the planet
Safety
100% human safe for touch and application
There is no primer or chemical compound that requires refrigeration, reducing your cost overhead and any associated safety risks.
As headlamps have become larger in EV models, non-reactive adhesives dramatically simplifies manufacturing.
Reactive adhesives are messy to apply, severely time-constrained, and practically irreversible when applied. Larger, wrap-around headlamps that are becoming more common in EV models require the kind of flexibility and simplicity only non-reactive adhesives can deliver.